Reinforcing Steel
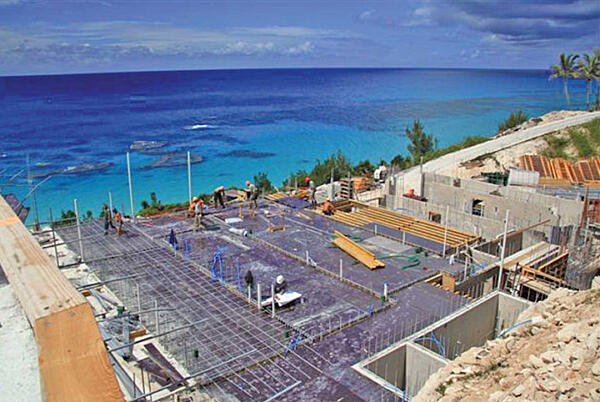
Reinforcing steel (rebar) is widely used in a variety of applications from bridges to reinforced buildings to enhance the tensile strength of the surrounding concrete. However, the addition of these strengthening elements can prove problematic for the structure if proper care is not taken to avoid corrosion. Because of the porous nature of concrete, moisture and road treatment chemicals can seep into the concrete, reaching the rebar within.
Exposed to these corrosive elements, the rebar will begin to develop rust corrosion products that are 2-10 times more voluminous than the original steel pieces. As these corrosion products continue to build, stress on the surrounding concrete increases until the surface begins to crack and spall. This can be dangerous for the vehicles, pedestrians, or wildlife below, and can weaken and compromise the stability of the bridge structure. Hot-dip galvanized reinforcing steel eliminates the risk of spalling, because the zinc corrosion products are less voluminous and migrate away from the bar into the matrix of the concrete. The migration alleviates the potential for increased pressure, thus eliminating the risk of spalling.
The deterioration of reinforced concrete structures, such as bridges, is estimated to cost more than $20 billion. Increasing by nearly $500 million each year, spalling and concrete deterioration have become a major liability for highway agencies. There is, however, a way to protect these infrastructure investments from the ravages of corrosion. Using hot-dip galvanized steel rebar for corrosion protection in concrete bridge elements, such as decking, piers, or piles, ensures they will resist spalling and stand strong for generations. Hot-dip galvanized steel rebar takes advantage of the inherent benefits of the metallurgical bond created during the galvanizing process. Galvanized rebar has a bond strength of 3,600 PSI, meaning when rebar is dropped, kicked, stepped on, or rubbed against existing concrete or other rebar pieces on the job site, the protective coating will remain tightly adhered. From installation through the use phase, galvanized rebar proves its tough, durable zinc coating can withstand the rough handling inherent in bridge or highway construction without succumbing to the damaging effects of corrosion.
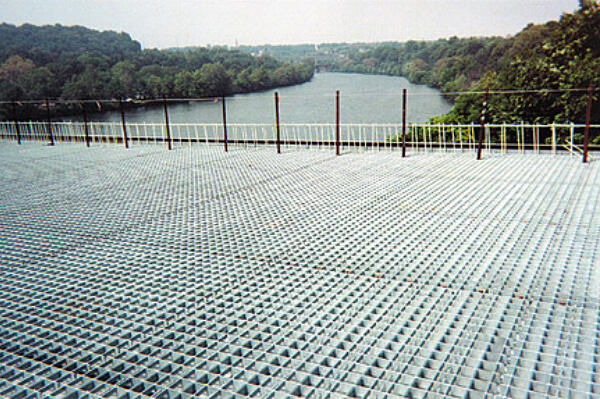
Exposure to the elements is a given for any bridge and highway construction site, and this can be problematic for rebar lying in wait. Epoxy coated rebar is particularly susceptible to UV damage, where the coating immediately begins breaking down under UV ray exposure. This means the corrosion protection of this type of rebar is compromised before it even enters service. Epoxy coated rebar may also crack when handled in temperatures less than 50 F, limiting and perhaps even delaying installation due to chilly weather.
Galvanized steel rebar will not be damaged by the sun's rays as it waits for implementation. The durable zinc coating will withstand the effects of UV light, as well as exposure to rain or snow, protecting the rebar both as it waits and in use. Similarly, cold temperatures will not in any way affect the coating, meaning galvanized rebar is ready for use when you are.
View More Reinforcing Steel Case Studies
Reinforcing Steel Story
Galvanized Steel Stories: New York State Thruway Authority- Galvanized Rebar
Learn more about galvanized rebar and earn continuing education credits by requesting an in-person seminar or taking our online rebar seminar.