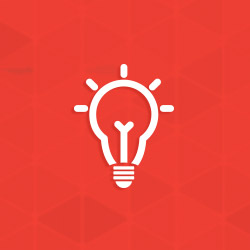
Steel Reactivity with Silicon and Phosphorus
What is the correct formula for determining steel reactivity when I have silicon and phosphorous in incoming steel?
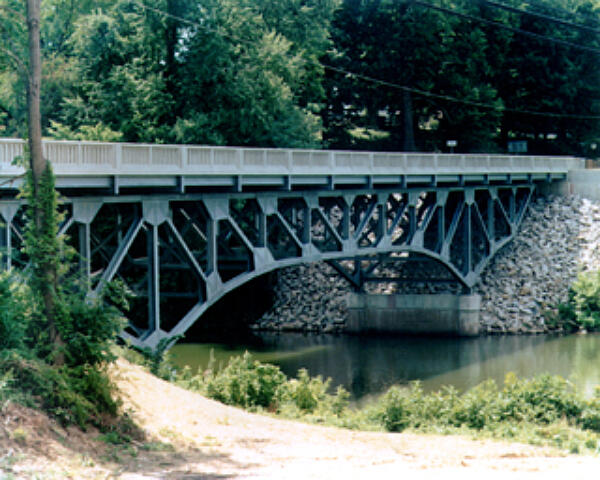
This is a very tricky question. The original authority on the subject of silicon reactivity was Robert W. Sandelin who found that the rates of enhancement of reaction-diffusion peaked at a silicon concentration of about .10% wt%. The graph below shows the relationship between zinc coating thickness and silicon content of the steel as researched.
Silicon changes the diffusion reaction between zinc and iron. When low silicon material is galvanized, the diffusion reactions take place in the first few minutes of immersion in the galvanizing bath. The process slows rapidly after about six or seven minutes and the coating will not increase in thickness even with much longer immersion times.
The high silicon steel continuous to pick up zinc in a linear fashion as the coating time increases. This can cause some very thick coatings on steel parts. The silicon is acting as a catalyst to promote the interdiffusion of iron and zinc which leads to the formation of a very thick layer to intermetallic. The layer that grows is the delta intermetallic, which is 90% zinc and 10% iron. The thick intermetallic layers tend to be more brittle and have a greater likelihood of experiencing handling damage. If the silicon is not evenly distributed on the base steel, there can be significant thickness differences in the galvanized coating. Intermetallic crystals may reach the surface of the coating and result in a dull gray surface or even a mottled surface that may be aesthetically unacceptable.
The presence of intermetallics at or near the coating surface and their relatively open coating microstructure can lead to the erroneous conclusion that the part is falling apart. Research carried out by the University of Cardiff in Wales for ILZRO project took an in-depth look at the problem of silicon reactivity and included phosphorous as a reactive element, also. The researchers varied the weight percentage of silicon and phosphorous and then assessed the reactivity of the steel at different galvanizing temperatures. This work has led to a new table of reactivity classifications for silicon and phosphorous content. One interesting finding is that even when the silicon content is low, steel class 3, if the phosphorus content is high the steel is very reactive. The last column of the table indicates that the coatings with high phosphorous have the greatest tendency to flake off of the steel.
© 2025 American Galvanizers Association. The material provided herein has been developed to provide accurate and authoritative information about after-fabrication hot-dip galvanized steel. This material provides general information only and is not intended as a substitute for competent professional examination and verification as to suitability and applicability. The information provided herein is not intended as a representation or warranty on the part of the AGA. Anyone making use of this information assumes all liability arising from such use.