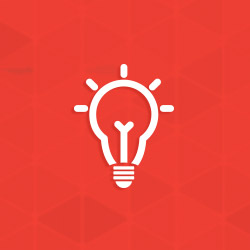
Inspection of Products - Coating Thickness Measurements
I have an inspector who wants to measure the coating thickness of a large assembly by taking all of his readings on one small bracket and declaring that the whole assembly does not meet specification. What do I tell him?
The hot-dip galvanized coating thickness requirement is dependent on the thickness of the base steel material. ASTM A123 and ISO1461 both give coating thickness tables to determine the value appropriate for a particular steel article. Table 1. from ASTM A123 gives a category of steel materials as well as the steel thickness range to determine the Minimum Average Coating Thickness Grade. The steel material categories describe the type of steel product to be hot-dip galvanized. The thickness requirement for the galvanized coating is given by the thickness grade in the table. The thickness grade is a direct reflection of the coating thickness in micrometers. The coating thickness can be measured by four separate techniques: magnetic thickness gauge, stripping method, weighing before and after galvanizing, and optical microscopy. Coating thickness is often expressed as weight per unit area and this ratio is related to the density of zinc at room temperature, 7.133 gm/cm3. Some of the measurement techniques take advantage of the relationship between coating thickness and coating weight to measure the weight added to the steel article and, thereby, determine the coating thickness value. The most popular measurement technique for galvanized coating thickness is the magnetic thickness gauge.
Table 1: Minimum Average Coating Thickness Grade by Material Category | ||||||
---|---|---|---|---|---|---|
All Specimens Tested, Steel Thickness Range (Measured) in. [mm] | ||||||
Material Category | <1/16 [<1.6] | >1/16 to <1/8 [>1.6 to <3.2] | >1/8 to 3/16 [>3.2 to < 4.8] | >3/16 to <1/4 [>4.8 to <6.4] | >1/4 to <5/8 [>6.4 to <16.0] | >5/8 [>16.0] |
Structural Shapes | 45 | 65 | 75 | 75 | 100 | 100 |
Strip and Bar | 45 | 65 | 75 | 75 | 75 | 100 |
Plate | 45 | 65 | 75 | 75 | 75 | 100 |
Pipe & Tubing | 45 | 45 | 75 | 75 | 75 | 75 |
Wire | 35 | 50 | 60 | 65 | 80 | 80 |
Reinforcing Bar | -- | -- | -- | -- | 100 | 100 |
Forgings and Castings | -- | -- | -- | 100 | 100 | 100 |
Magnetic gages measure either the magnetic attraction between a magnet and a magnetic material such as steel or measure the magnetic flux change through a coating to a magnetic steel substrate. The methodology for using this type of gage is contained in ASTM E376. Magnetic thickness gages have been studied a number of times The conclusions are very consistent that the gages are accurate to within 3 to 10 micrometers. More expensive gages are more accurate. These types of gages should be calibrated often to retain their accuracy and repeatability. Magnetic thickness gages are very accurate on flat surfaces but are inaccurate on curved surfaces. Surface roughness can also reduce the accuracy of the thickness readings.
The second method for determining galvanized coating thickness is the Stripping Method for determining coating weight detailed in ASTM A90. This test is a destructive procedure that first weighs the sample with the zinc coating on the surface. Then the coating is stripped from the steel surface and the sample is weighed again with no galvanized coating on the surface. The difference in the two weights is the weight of the coating. In order to find the coating thickness, the weight of the coating must be used with the surface area of the article and the density of zinc.
One of the inaccuracies with this method is that the galvanized coating contains iron as well as zinc. Both of the materials in the coating are stripped from the sample. In sheet galvanizing there is very little iron-zinc alloy but in batch hot-dip galvanizing there is a considerable amount of alloy coating. The Iron has a slightly different density than zinc so calculating the coating thickness based on the weight change will give a slightly higher coating thickness than the actual value. The third technique for determining the hot-dip galvanized coating thickness is Weighing Before and After Galvanizing. The coating weight is obtained by subtracting the weight before galvanizing from the weight after galvanizing. Using the surface area and the density of zinc, the coating thickness can be calculated from the coating weight. This method actually measures the weight of zinc metal added to the steel particle.
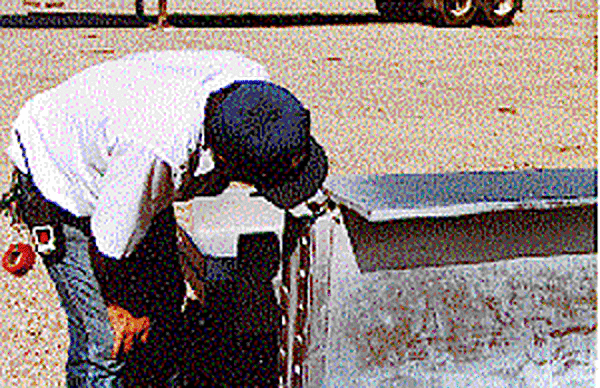
The coating contains iron-zinc inter metallic so the actual coating contains more weight than just the zinc metal alone. This means that this method will underestimate the coating thickness by as much as 10% in many cases. The surface area must also be accurately determined for this method to be accurate. the weight measurement before galvanizing must be done after the article is cleaned and dried so that there are no excess fluids on the surface of the part and all of the iron oxides have been removed. One of the disadvantages of this technique is that when several different types of steel parts are assembled into a fabricated structure prior to galvanizing, the weighing method gives an average for the entire assembled does not differentiate each type of part as required by the specification.
The fourth technique for determining the hot-dip galvanized coating thickness is Optical Microscopy in accordance with ASTM B487. The coating thickness is measured by cutting out a portion of the coated steel, mounting it, and preparing the edge of the mounted piece for optical microscope examination. The test method details the conditions that need to be met to have an accurate reading of the coating thickness. There is skill involved with mounting and polishing the piece of coated steel to get the most accurate reading of coating thickness. This method is a destructive test so it may not be appropriate for all galvanized articles.
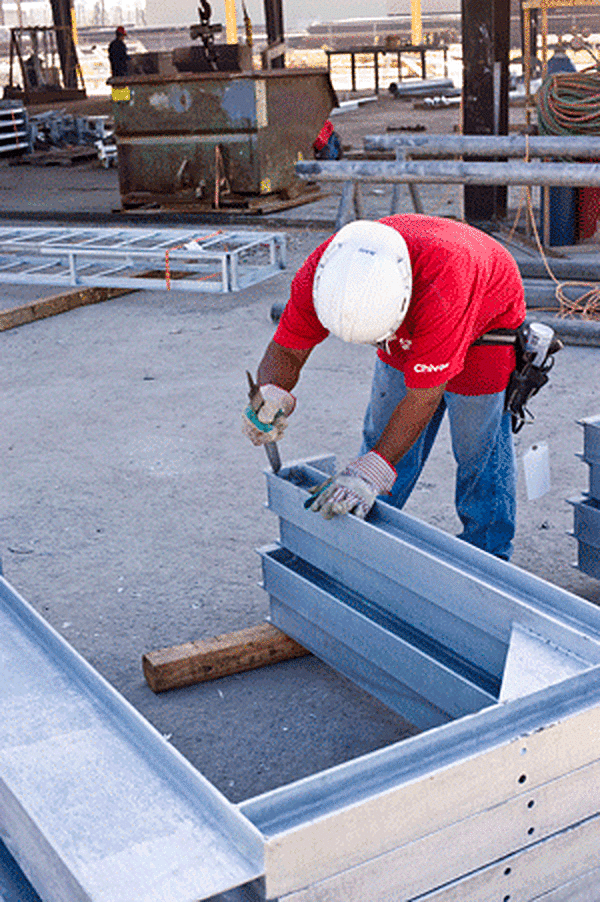
Sampling
Specification ASTM A123 calls for an average coating thickness to be a minimum of a specific value. The average is obtained in different ways depending on the size of the galvanized article. For small galvanized articles whose surface area is less than 1000 cm2, each individual piece shall be considered a test article and shall have no less than five measurements made of its coating thickness. The average of those five measurements shall be considered a specimen coating thickness and shall be not less than one coating grade below the required coating grade for the material. The average of the appropriate number of specimens shall be greater than the required coating grade for the material. So if there were 100 pieces of galvanized steel, a minimum of three pieces must be measured and their specimen coating thickness measurements must be averaged to determine the coating thickness for the lot.
For large galvanized articles whose surface area is greater than 1000 cm2, each individual piece shall be considered to be three sections for measurement purposes. Each section shall be treated as an individual specimen. In each section five widely separate measurements shall be taken to represent the overall coating thickness. This means that many measurements in a specific location do not represent the part's average coating thickness. The number of measurements may exceed five but may not be less than five in each section of the part. The average of these five or more measurements shall be treated as a specimen coating thickness value and shall not be less than one coating grade below the required coating grade for the material. The average of the three sections shall be considered the overall coating thickness and shall be greater than the required coating grade for the material.
For fabricated articles that have a mixture of different parts welded together to make a single fabricated structure, the coating thickness of each different type of material must be treated separately. for instance, a large sign structure may be comprised of different size tubing or pipe and have brackets or cross-bracing that is different thickness steel. All of the parts must be measured according to their material category and, if there are a number of brackets, all of the brackets must be treated as if they are tied together. The sampling procedures are intended to produce the most reasonable average coating thickness while still giving a statistically significant number of the coating thickness
© 2025 American Galvanizers Association. The material provided herein has been developed to provide accurate and authoritative information about after-fabrication hot-dip galvanized steel. This material provides general information only and is not intended as a substitute for competent professional examination and verification as to suitability and applicability. The information provided herein is not intended as a representation or warranty on the part of the AGA. Anyone making use of this information assumes all liability arising from such use.