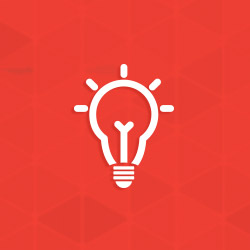
Dulling Galvanized Steel
What do I tell my customer when he says he wants to take off the bright shine I worked so hard to produce?
This question was first asked many years ago in the electrical transmission line business when electrical towers were erected in rural/wilderness areas. In the early 1970's, there were four separate power companies/agencies who demanded galvanized products be dulled, that is, their reflectivity needed to be reduced to 12% to 18% before installation in the field. A newly galvanized part with the normal pure zinc layer on the outside has a natural reflectivity of over 70% in the visible range. The natural reflectivity of aluminum is around 80- 85%. If the part has an outer layer of intermetallic, the reflectivity is greatly reduced. This reflectivity change will also happen over time as the galvanized part weathers and the zinc oxides and carbonate films form on the surface of the part.
The Bonneville Power Administration, a Department of Interior Branch, in the Washington state area sent a letter t o many galvanizers and to the AGA, on the need for reducing the reflectivity of galvanized parts due to safety and environmental concerns. Drivers may be flash blinded by brightly reflecting galvanized electrical towers and ecologists contended that bright electrical towers in rural and wilderness areas were disruptive to the environment
A number of methods have been suggested to accomplish the task of dulling the bright surface of newly galvanized parts. One of the first methods produced "black coatings" by dissolving three pounds of copper sulfate crystals in a gallon of water, then adding a half pint of concentrated hydrochloric acid. This mixture was sprayed onto the surface of newly galvanized parts and immediately rinsed off since it acted very quickly. Another possible method of dulling the surface is to dip the parts in a 1% nitric acid solution for 90 seconds. A third method is to apply a primer coat to the surface of the galvanized steel; there are a number of commercially available primer coats that will darken the surface adequately. These primers can be spray applied in the field. Another method to dull the surface is to zinc phosphate treat or phosphatize a newly galvanized part. With all of these methods, it is important to note that, if the parts are quenched, a chromate conversion coating will change the outer surface and make the dulling treatment ineffective.
There are some practices that can be performed during the galvanizing process that may be able to dull the surface of the parts without further treatment
- A very slow cooling rate, no quenching: will allow the intermetallic to grow even after removal from the bath.
- The use of little or no brightener bar in the bath will give a duller coating.
- Over-pickling the parts will also give a duller appearance.
- The use of steel that is high in silicon content will also give a coating that is nearly all intermetallic and, therefore, dull gray in appearance.
These processing techniques will not produce a galvanized coating with 12% to 18% reflectivity in all instances so they should only be used after agreement with your customer. An interesting method for dulling galvanized parts was found when galvanized steel was stacked on green wood and the tannic acid from the wood stained the newly galvanized parts brown. There is no established practice using tannic add to dull the surface of new parts but we may one day see common tea used as a quench for parts to give a low reflectivity coating. This could be the first "Nestea plunge" for galvanized parts.
© 2024 American Galvanizers Association. The material provided herein has been developed to provide accurate and authoritative information about after-fabrication hot-dip galvanized steel. This material provides general information only and is not intended as a substitute for competent professional examination and verification as to suitability and applicability. The information provided herein is not intended as a representation or warranty on the part of the AGA. Anyone making use of this information assumes all liability arising from such use.