Tubular Fabrications
Tubular assemblies (handrails, pipe columns, pipe girders, street light poles, transmission poles, pipe trusses, sign bridges) are commonly galvanized to provide interior and exterior corrosion protection of the product. Hollow products require proper cleaning, venting, and drainage in order to grow an optimal galvanized coating.
Steel is immersed and withdrawn from the kettle at an angle, so vent holes are located at the highest point and drainage at the lowest. Sections of fabricated pipe-work should use full open-tee or miter joints at interconnections. Vent holes must be provided at each end of every enclosed section.
Most galvanizers prefer to visually identify venting from the outside, in order to verify the adequacy of the venting as well as to determine that venting has not been mistakenly omitted.
Some galvanizers may hesitate to process complicated pipe assemblies unless all venting is visible on the outside and readily accessible for inspection. The diagram below illustrates recommended designs for tubular fabrications and hollow structures.
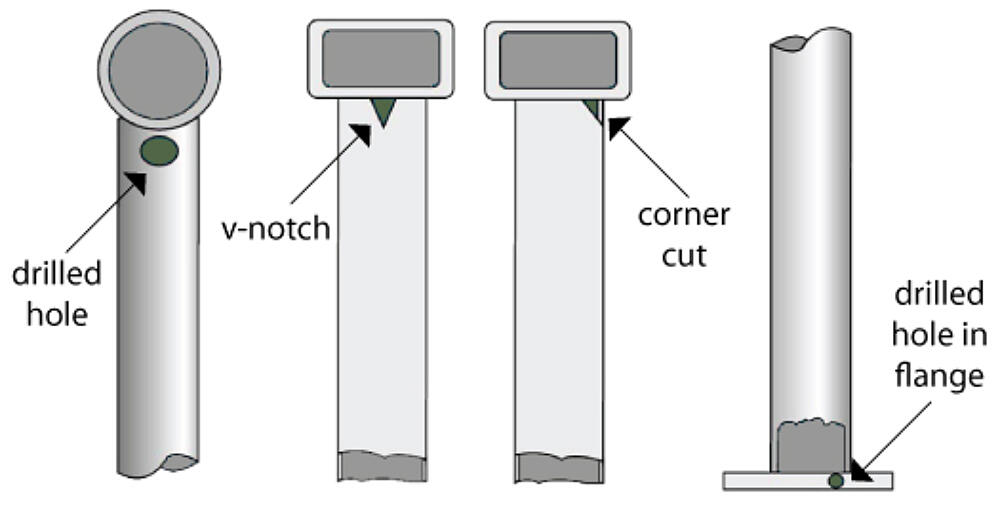
Base-plates and end-plates must be designed to facilitate venting and draining. Fully cutting the plate provides minimum obstruction to a full, free flow into and out of the pipe. Since this is not always possible, using vent holes in the plate often provides the solution.
Vent holes can be plugged after galvanizing, but are frequently left open. If the holes will be plugged after galvanizing, the method of venting should be kept in mind.
It is recommended tubular structures be completely submerged in one dip into the galvanizing kettle. This minimizes potential internal coating problems that, because of the size and shape of the item, may be difficult to discover during inspection.