In the Field
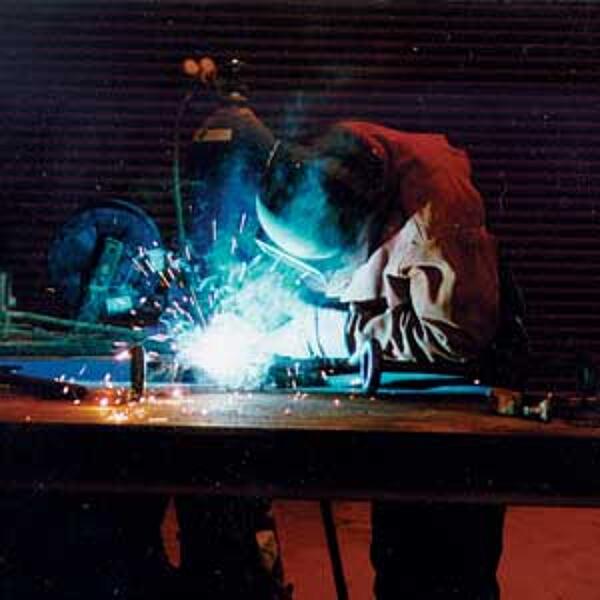
Welding
Welding galvanized reinforcement does not pose any problems, provided adequate precautions are taken. Steps include utilizing a slower welding rate and maintaining proper ventilation (ventilation normally required for welding operations is adequate). More details are outlined in the AGA's Welding and Hot-Dip Galvanizing publication.
Installation and Handling
HDG can be handled in all temperatures. Epoxy coated rebar may crack when handled in temperatures less than 50 F. Galvanized reinforcing steel can be handled and placed in the same manner as black steel rebar because of its superior abrasion resistance. The zinc coating of HDG rebar is harder than the steel itself. Bundling, dragging, and rough treatment prior to and during placement have no detrimental effect. Epoxy coated rebar requires delicate handling to prevent damage to the epoxy coating. Any damage to the coating prior to placement will compromise the corrosion protection.
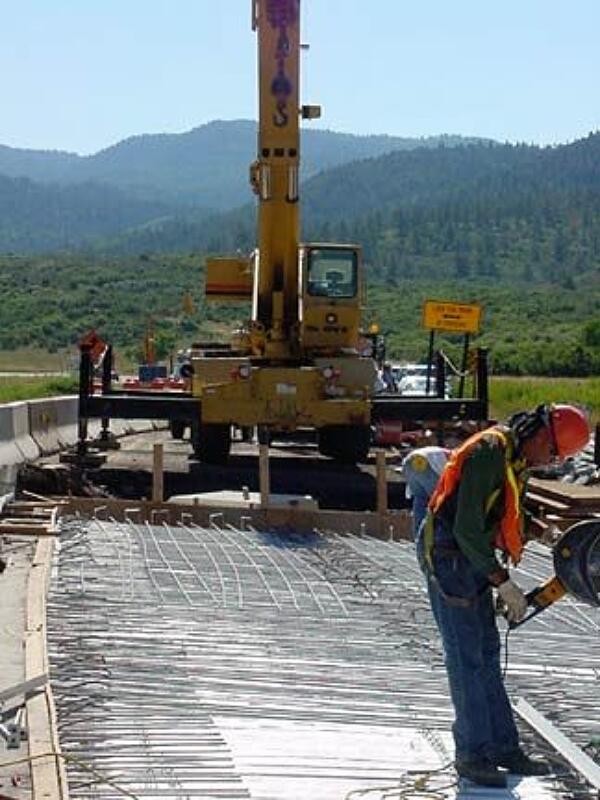
Storage
Galvanized bars can be stored outside without any degradation in corrosion performance from UV light. The ease of storage makes it feasible to store standard lengths of galvanized reinforcement so it is available on demand. (Please refer to the AGA's publications Hot-Dip Galvanizing vs. Epoxy-Coated Rebar or Field Handling Guide: Hot-Dip Galvanizing vs. Fusion Bonded Epoxy for additional information).
Overlap lengths
Detailing of galvanized reinforcing steel should conform to the design specifications for uncoated steel bars and to normal standard practice consistent with the recommendations of CRSI. Overlap lengths of hot-dip galvanized reinforcing steel are identical to uncoated steel rebar because of the equivalent bond strength to concrete. Laboratory tests show no significant difference in the slip for HDG and black rebar in loaded bars. American Concrete Institute (ACI 318) recommends 20% more overlap when using epoxy-coated rebar.
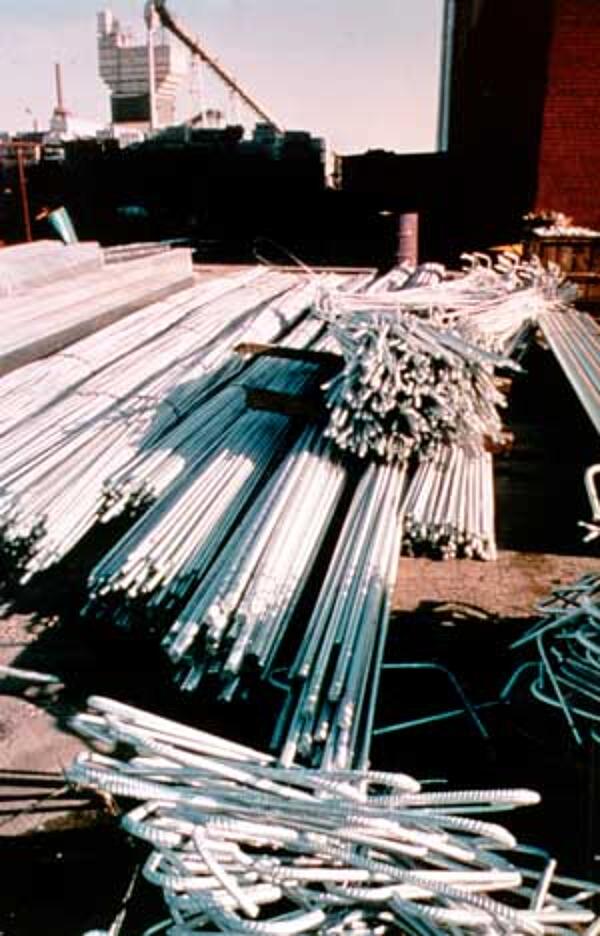
Touch Up and Repair of Coating
Local removal of the galvanized coating in the area of welds, bends, or sheared ends will not significantly affect the protection offered by galvanizing, provided the exposed surface area is small compared to the adjacent surface area of galvanized steel. When the exposed area is excessive and gaps are evident in the galvanized coating, the area can be repaired in accordance with ASTM A780. Although galvanized coatings are highly abrasion resistant, coating damage may occur once the galvanized steel leaves the galvanizers facility due to extremely rough handling, installation techniques, or in-service conditions. There are methods available to ensure post-galvanizing coating integrity. There are three widely available accepted touch-up and repair methods: zinc-rich paint, zinc-based solder, and metallizing.
Zinc-rich paint
Organic or inorganic zinc-rich paint for touching up and/or repairing galvanized steel should contain between 65-69% zinc by weight, or >92% by weight metallic zinc in the dry film. Inorganic zinc-rich paints are more effective than organic in terms of delivering corrosion protection, and they do not shrink after drying/curing as organic coatings do. This is a major advantage when the paint is applied to corners, edges and rough surfaces.
Zinc-rich paint is brush- or spray-applied to a clean, dry steel surface. Spraying or brushing should be in a single application of multiple passes according to the paint manufacturers instructions. Zinc painting can be done on the job-site and is the easiest repair method to perform because limited equipment is required.
Zinc-based solder
Soldering with zinc-based alloys consists of applying zinc alloy -in stick or powder form -to the area to be repaired, which has been preheated to approximately 600 F (315 C). Common repair solders include zinc-tin-lead, zinc-cadmium, and zinc-tin-copper alloys.
The surface to be reconditioned shall be wire-brushed, lightly ground, or mild blast-cleaned. All weld flux and spatter must be removed by mechanical methods if wire brushing or light abrasive-blasting is inadequate. The cleaned area should be preheated to 600 F (315 C) and wire-brushed at the same time. Care must be taken to not burn the surrounding galvanized coating. When the repair has been completed, flux residue can be removed by water rinsing or wiping with a damp cloth.
Metallizing
Metallizing is the melting of zinc powder or zinc wire in a flame or electric arc and projecting the molten zinc droplets by air or gas onto the surface to be coated. The zinc used is nominally 99.5% pure or better. The performance of wire versus powder is comparable. Zinc-aluminum alloys also can be used. The application equipment used may limit the concentration of aluminum.
The AGA has an online video series for the Touch-Up and Repair of Hot-Dip Galvanized Steel. Six short videos detail the many aspects to consider when touching up or repairing HDG steel.
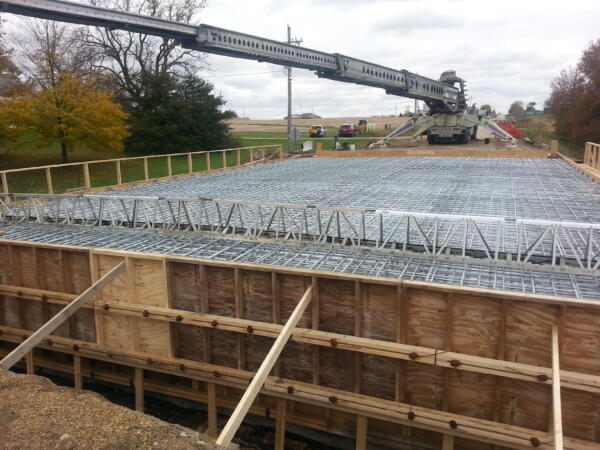
Removal of Forms
Metal forms should be electrically isolated from the galvanized rebar to prevent dissimilar metal reactions during the concrete curing. If metal forms are not isolated from the galvanized rebar, then zinc ions can be released from the galvanized coating to try to protect the metal form, resulting in a change in the concrete appearance near the galvanized bar placement.
Because cement with naturally low occurring levels of chromates may react with zinc, it is important to ensure that forms and supports are not removed before the concrete has developed the required strength to support itself. Normal form removal practices may be utilized if the cement contains at least 100 ppm of chromates in the final concrete mix or if the hot-dip galvanized bars are chromate-passivated according to ASTM A767.