Size Considerations
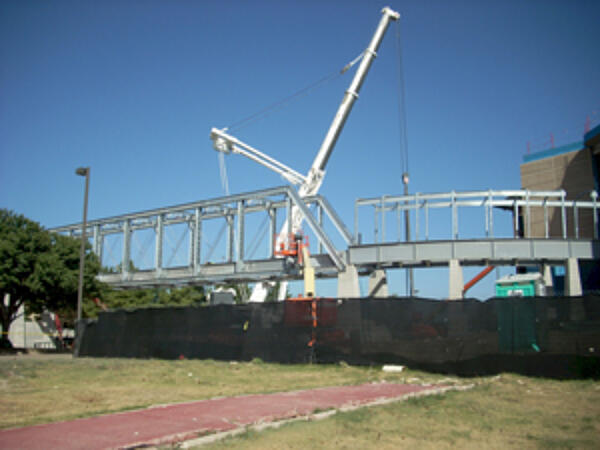
As the size, number, and weight of vehicles on the road continues to grow, bridge designs have expanded to accommodate this traffic. Hot-dip galvanizing is a complete immersion process, which means the parts must fit in the zinc bath to be coated. In North America, the average kettle length is 40 feet (there are many 50-60 foot kettles), with depths ranging from 6-12 feet, and widths of 5-8 feet. Although there are size constraints based on the size of the zinc bath, there are a few options to galvanize larger spans.
Modular Design
The easiest way to galvanize larger spans is to design the bridge in modules or sub-units to fit in the galvanizing kettle. Designing the pieces to fit in the galvanizing bath in one pass eliminates the challenges from progressive dipping, reduces the potential for warpage, and provides additional savings in manufacturing and assembly because of simplified handling and transportation. The sub-units can be connected after galvanizing by field-welding or bolting. A great example of a bridge utilizing galvanized sub-units is the Stearns Bayou Bridge.
Modular design can also provide advantages when accelerated bridge design is desired. One innovative design, developed and tested by the Bridge Technology Center within the Short Span Steel Bridge Alliance (SSSBA) is the press-brake-formed tub girder (or folded plate). This modular design would allow a galvanized tub to be precast with a deck and shipped to the site to lay in place. The first short span bridge utilizing this technology, the Amish Sawmill Bridge, was opened in Fairbank, Iowa in January 2016.
Modular Design Case Study
Stearns Bayou Bridge - Ottawa County, MI, 1966
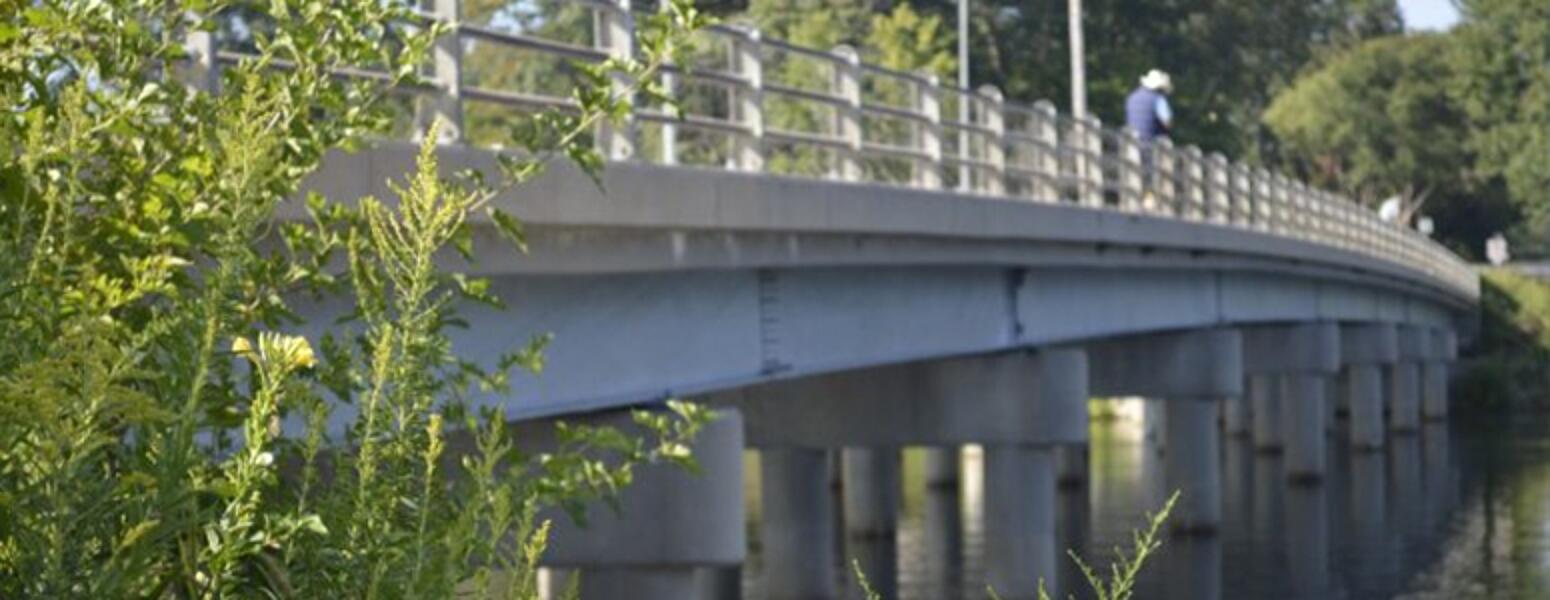
The Stearns Bayou Bridge, installed in 1966, is believed to be the first fully galvanized bridge in the United States. The bridge is 420 feet long, consisting of two 60-foot and six 50-foot spans, a 30 foot roadway, and five foot walkway on each side. In addition to the beams, all diaphragms, bearing pads, handrail, and shear connectors were also hot-dip galvanized. An inspection in 1997 revealed the galvanized steel to still be in good condition with mild staining and no visible rust. Coating thickness measurements were taken on the bridge, and were as follows:
Sample Area | Coating Thickness (mils) | Projected Time to First Maintenance |
---|---|---|
Beams/Diaphragms | 6.3 | >95 Years |
Bearing Pads | 2.9 | 95 Years |
Handrails | 1.9-4.6 | 65-95 Years |
In the rural environment, even with the harsh winters in Michigan, which lead to salt, standing water, and snow pile up on the galvanized steel, the bridge was projected to last at least another 65 years in 1997, which would be 2062, essentially giving the Stearns Bayou Bridge a minimum 100-year life.
Progressive Dipping
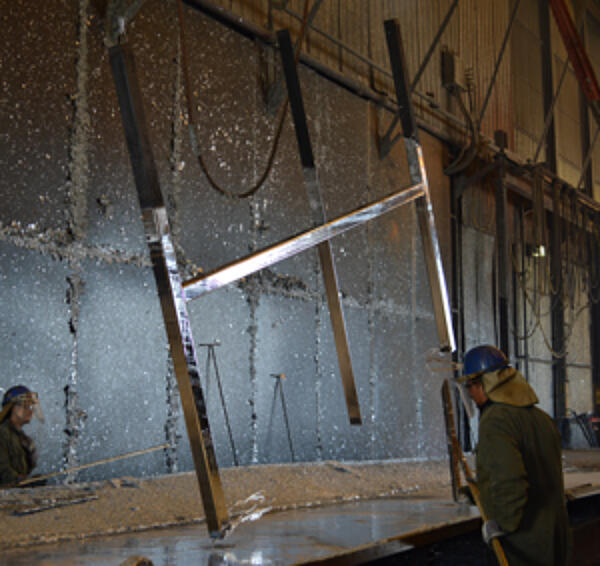
If modular units aren’t possible or still too large, the dimensions of the kettle are not the actual maximum size of pieces that can be galvanized, as pieces can be progressively dipped. Progressive dipping is simply the process of coating the steel part in two passes. In other words, if half of the piece can fit in the bath, the part can be galvanized on one side, rehung, and then dipped on the remaining surface. In essence, this would nearly double the size of part that can be coated.
There are some unique challenges when it comes to progressive dipping, and it is crucial to have communication with the galvanizer early in the design phase to minimize these concerns. When steel is heated, it expands, and as it cools it contracts; therefore, when a part of a steel article is heated and the other part is cool, there is an increased risk for distortion. The galvanizer will be able to provide recommendations to minimize this concern, as well as verify any weight or building constraints to processing the piece at their specific facility. Progressively dipped pieces often have an overlap area that is visible on the piece. The line or darker area is purely cosmetic, and will fade over time as the coating weathers naturally. However, the overlap area will most likely have a thicker coating, so it is important to consider this if the area will be an important connection point with other pieces.
Complementary Coatings: Metallizing & HDG
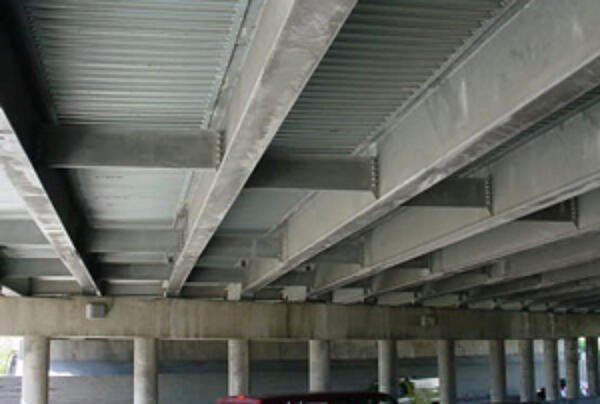
Hot-dip galvanizing and zinc spray (metallizing) can be used in tandem on large or complex structures. Zinc spraying, or metallizing, is accomplished by feeding zinc wire or powder into a heated gun where it is melted and sprayed onto the part using combustion gases and/or auxiliary compressed air. The 100% zinc coating can be applied in the shop or the field to any size part, and is often sealed with a low viscosity polyurethane, epoxy-phenolic, epoxy, or vinyl resin. Because both coatings are comprised of zinc, there is no concern for galvanic corrosion present when dissimilar metals are connected.
Because metallizing requires specialized equipment and a skilled operator, it is expensive initially. Hot-dip galvanizing smaller parts of the bridge, or dipping the ends of larger pieces and metallizing the center are common practices as galvanizing provides economic efficiencies. Furthermore, the two coatings have similar appearances both initially and as they weather, providing the bridge with a cohesive look. Finally, if the metallized coating is applied properly and thick enough, the corrosion performance will be similar to hot-dip galvanized steel. The Castleton Bridge in Indiana (below) is a great example of a bridge currently using both hot-dip galvanized and metallized steel.
Complementary Coatings Case Study
Castleton Bridge - Castleton, IN, 1970
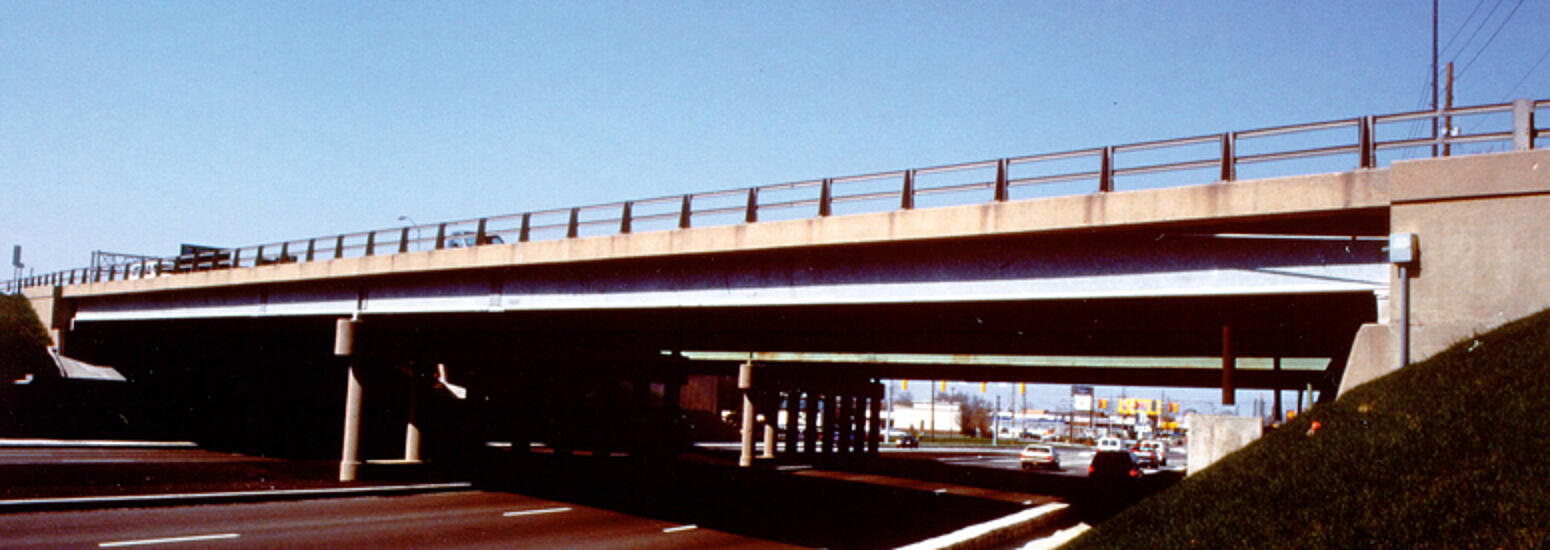
The Castleton Bridge, constructed in 1970 in Indiana, demonstrates the use of hot-dip galvanizing and metallizing together in a unique way. Typically, the two coatings are used on the same piece, in a planned, purposeful way, such as to cover the middle of a beam that is too large to be fully galvanized, even when using progressive dipping.
When the Castleton Bridge was built, the southbound side was painted and the northbound side was galvanized, for research purposes. After 14 years, the painted side required repainting, while the galvanized side remained untouched. Then, in 2002, the painted side was in need of repair again. This time the Indiana DOT elected to metallize the girders, based on the performance of the hot-dip galvanized southbound sections.
In 2011, the metallized and galvanized girders were both inspected and continue to perform well. The hot-dip galvanized girders have not required maintenance throughout the 41 years of service, and still have enough zinc present to meet the minimum coating thickness requirements in ASTM A123. Similarly, since metallizing in 2002, the northbound bridge has not required any additional maintenance.