Longevity
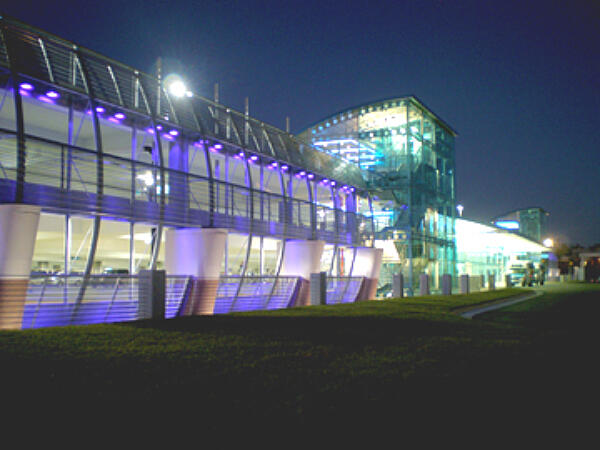
Hot-dip galvanized steel is often utilized in some of the harshest environments imaginable, yet it provides maintenance-free longevity for decades. The corrosion resistance of hot-dip galvanizing varies according to its surrounding environments, but generally corrodes at a rate of 1/30 of bare steel in the same environment. Measurements of the actual consumption rate of the coating during the first few years of service provide good data for projecting a conservative estimate for the remaining life to first maintenance, because as zinc corrosion products build on the surface, which in most environments are adherent and fairly insoluble, the corrosion rate often slows as time progresses.
Whether exposed in the atmosphere, subjected to blazing UV rays, snow, and/or other elements, submerged in water, or embedded in soil or concrete, hot-dip galvanized steel can withstand the different corrosive elements and fulfill the intended design life. More information about hot-dip galvanized steels longevity can be found in the AGAs publication Performance of Hot-Dip Galvanized Steel Products.
In the Atmosphere
The most common exposure environment for hot-dip galvanized steel is atmospheric. As hot-dip galvanized steel is exposed to the atmosphere, the zinc interacts with free flowing air and moisture to develop the zinc patina. The zinc patina is critical to the longevity of galvanized steel in the atmosphere; and thus, accelerated, salt-spray tests that do not mimic real world exposure conditions are not an accurate predictor of HDGs longevity.
The performance of atmospherically exposed hot-dip galvanized steel depends on five main factors: temperature, humidity, rainfall, sulfur dioxide (pollution) concentration in the air, and air salinity. None of these factors can be singled out as the main contributor to zinc corrosion, but they all play a role in determining the corrosion protection hot-dip galvanized (zinc) coatings can provide in certain atmospheric conditions.
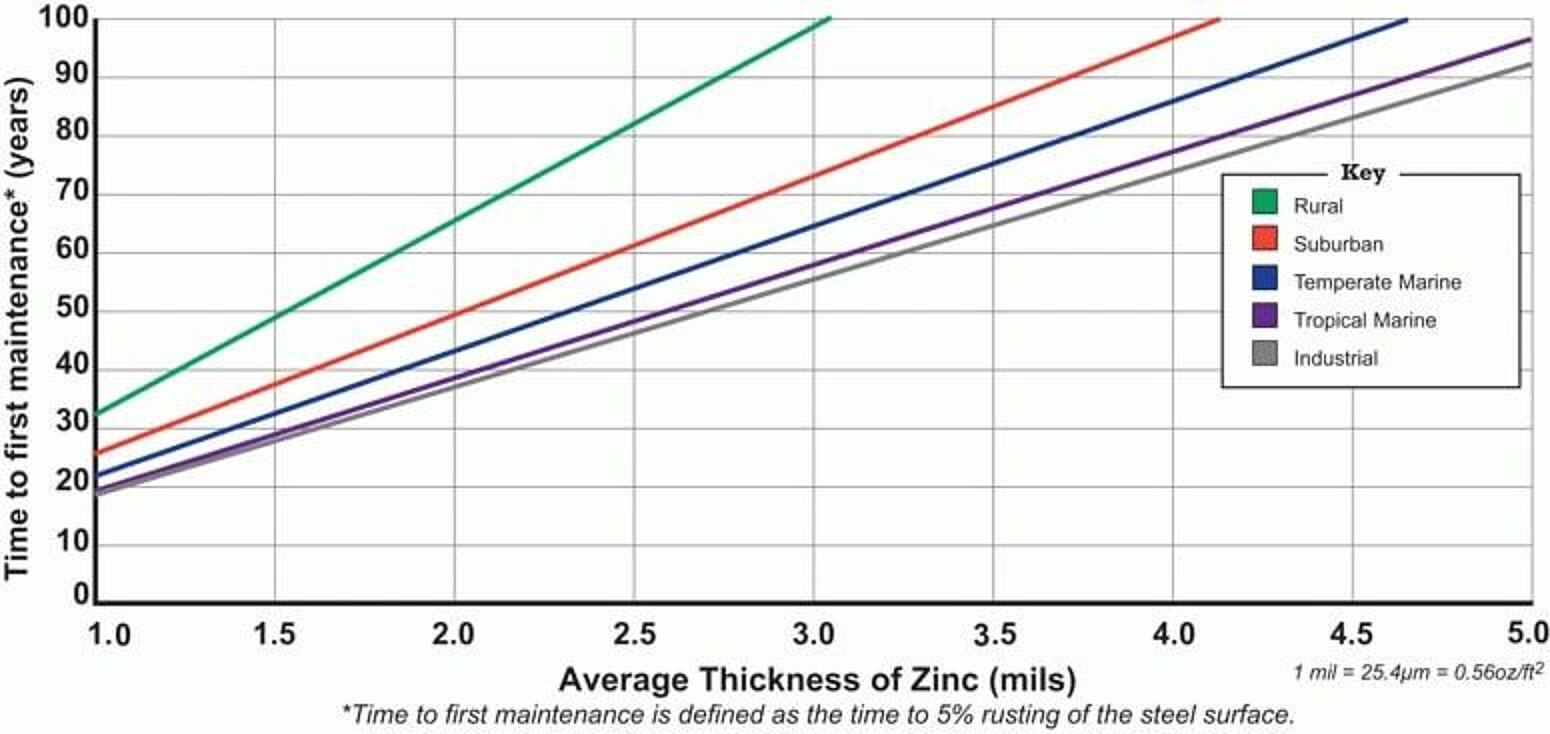
Time to First Maintenance
For nearly a century, independent and industry testing of samples in five environments (industrial, rural, suburban, tropical marine, and temperate marine) have yielded real-world performance data for hot-dip galvanized steel. Using this real-world corrosion data, statistical methods, and neural network technology, Dr. Gregory Zhang of Teck Metals Ltd. developed the Zinc Coating Life Predictor (ZCLP) to estimate the life of hot-dip galvanized coatings in atmospheric conditions. Using the ZCLP, you can input specific parameters for any environment and get an estimated time to first maintenance (TFM) for the galvanized coating.
Time to first maintenance is defined as 5% rusting of the base steel surface, which means 95% of the zinc coating is still intact, and an initial maintenance is recommended to extend the life of the structure. According to ASTM A123, the governing specification for hot-dip galvanizing, steel ¼-inch thick or greater must have at least 3.9 mils of zinc on the surface, but more often than not, there will be greater than the minimum requirement. Therefore, using the TFM chart, hot-dip galvanized structural steel (>1/4-inch thick) provides 72-73 years of life to first maintenance even in the most corrosive atmosphere, industrial.
In Soil
Another common exposure for hot-dip galvanized steel is partially or fully buried in soil. With more than 200 different types of soil identified in North America, hot-dip galvanizing's performance in soil is varied and hard to predict. The main factors that dictate the corrosivity of the soil are moisture content, pH level, and chlorides. These soil conditions are affected by additional characteristics such as aeration, temperature, resistivity, and texture or particle size. A general rule of thumb is galvanizing performs well in brown sandy soils, and not as well in gray, clay-like soils. This is because soil with larger particles wick moisture away from the surface more quickly so the galvanized piece has less exposure to moisture.
The first step to estimating the performance of hot-dip galvanized steel in soil is to classify it. And as the corrosion rate of steel in soil can range from less than 0.2 microns per year in favorable conditions, to 20 microns per year or more in very aggressive soils, misclassifying the soil can lead to unpredicted performance.
The AGA has developed a chart for estimating HDGs performance in soil based on real world corrosion data. In this case, service life is defined as total consumption of the coating plus 25%, and is an indication of when the structure should be replaced. There are four different charts based on the classification of the soil. Using the chart, the first classification is by chloride content — Charts 1 and 2 (top row) are used for soils with high chlorides (>20 PPM) and Charts 3 and 4 (bottom row) are used for soils with low chlorides (<20 PPM).
Once you have identified the chloride content, there is a second classification to determine the correct chart to use. For soils with high chlorides, the second determination would be moisture content. Soils with low moisture (<17.5%) fall on Chart 1, while soils with high moisture (>17.5%) fall on Chart 2. For low chlorides, the second determination is the pH level. Soils with high pH levels (>7.0) fall on Chart 3, while soils with low pH (<7.0) fall on Chart 4.
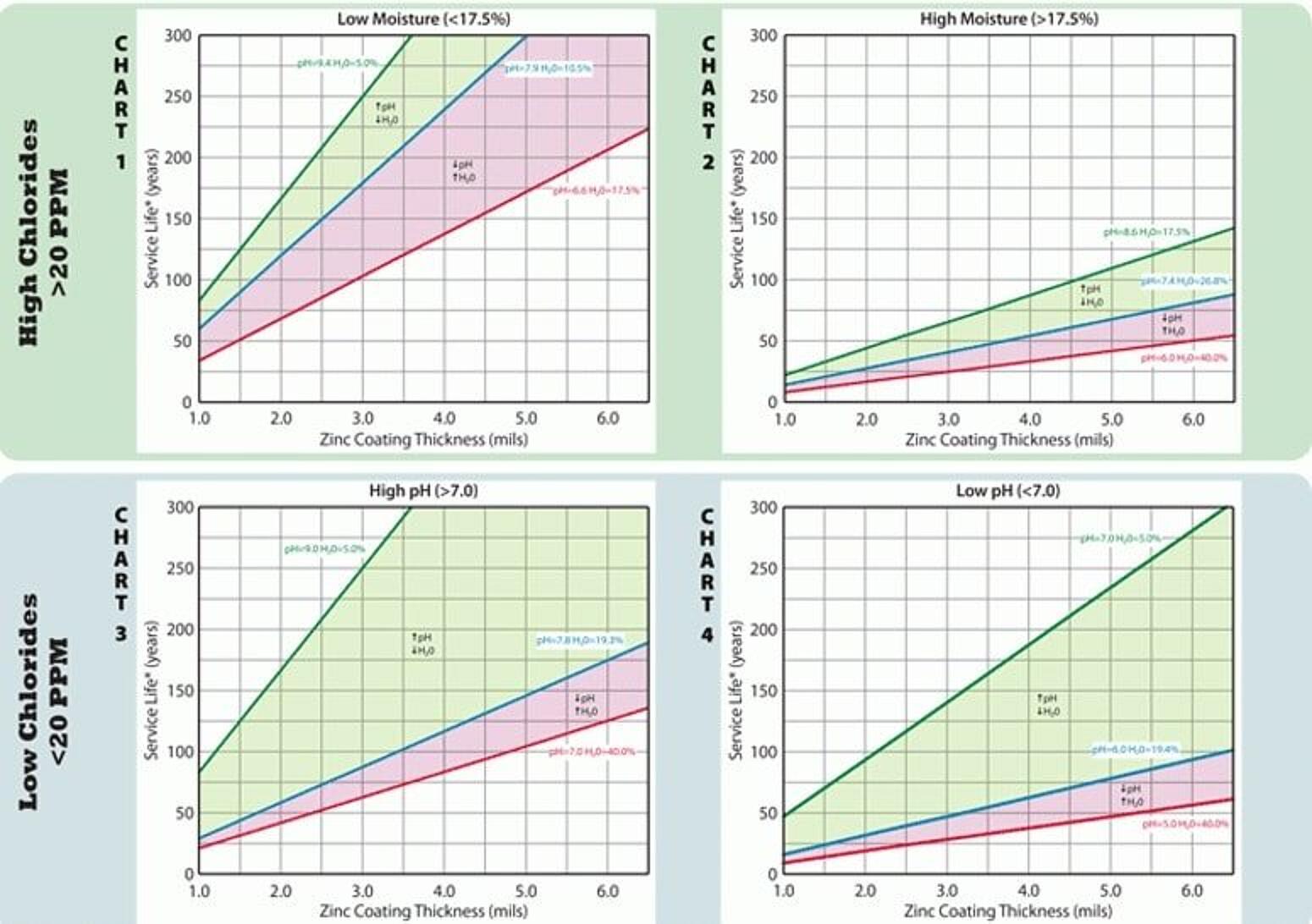
Once you are looking at the correct chart, the blue line represents the average for soils surveyed in that characteristic group, while the green line represents the best soil and the red line represents the worst soil in the category. The shaded areas show how the changes in pH and moisture content affect the estimated service life. Assuming 3.5 mils as a minimum thickness for HDG buried in soil, the chart shows the average life in the harshest soils (uncommon) would be approximately 50 years and in the best soils exceed 120 years.
Keep in mind unlike the atmospheric chart which shows time to first maintenance, this chart is predicting full service life (total zinc consumption + 25%) or time to replacement.
In Water
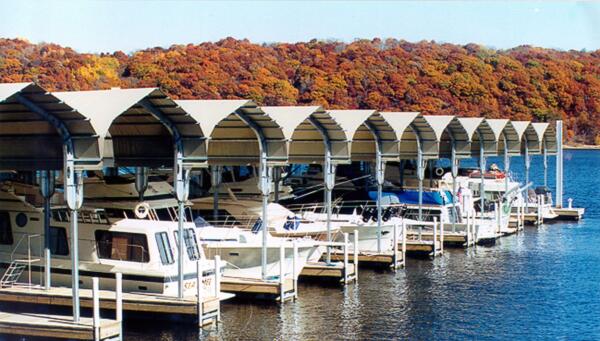
A less common environment for galvanized steel is submerged in or exposed to water. Moisture is highly corrosive to most metals including steel and zinc. However, because of the development of the passive, mostly non-soluble zinc patina, the corrosion rate of galvanized steel is much slower than bare steel. There are many different types of water (pure water, natural fresh water, potable water (treated drinking water), and seawater) and each has different mechanisms that determine the corrosion rate.
Similar to soils, the varieties of water make predicting corrosion rates difficult. Though pH level has the most profound effect, many parameters affect corrosion of metals in a water environment including oxygen content, water temperature, agitation, the presence of inhibitors, and tide conditions. Despite the difficulty of predicting corrosion, hot-dip galvanizing steel is one of the best methods of corrosion protection for submersed applications because of its complete, uniform coverage.
Water with high free oxygen or carbon dioxide content is more corrosive than water containing less of these gases, and hard water is much less corrosive than soft water. A natural scale of insoluble salts tends to form on the galvanized surface under conditions of moderate or high water hardness. The salts combine with zinc to form a protective barrier of calcium carbonate and basic zinc carbonate.
Similar to fresh water, galvanized coatings provide considerable protection to steel when immersed in sea water and exposed to salt spray. Influencing factors in the corrosion of zinc in fresh water also apply to sea water; however, the dissolved salts (primarily sulfides and chlorides) in sea water are the principal determinants of the corrosion behavior of zinc. Given the high level of chloride in sea water, a very high corrosion rate might be expected. However, the presence of magnesium and calcium ions has a strong inhibiting effect on zinc corrosion.
In Other Environments
Good Performance
There are a few other environments where hot-dip galvanized steel is traditionally used with great success:
- Chemical solutions with neutral pH (4-13)
- Treated wood (only HDG and Stainless are recommended)
- In Concrete
- Extreme Temperatures (-40 F to 392 F)
- In contact with Aluminum or Stainless (Except in salt water or salt water air environments)
Corrosive to HDG
A few environments especially corrosive to hot-dip galvanizing and are not recommended include:
- High pH > 13
- Low pH < 4
- In Contact with Dissimilar Metals
- Dependent on surface area and environment
- Best to isolate with non conductive material (rubber, cement, paint)
More information about hot-dip galvanized steels longevity can be found in the AGAs publication Performance of Hot-Dip Galvanized Steel Products.
Longevity Case Studies
Metrolina Greenhouses - Huntersville, NC, 1971
Frederick Meijer Botanical Gardens - Grand Rapids, MI, 1994
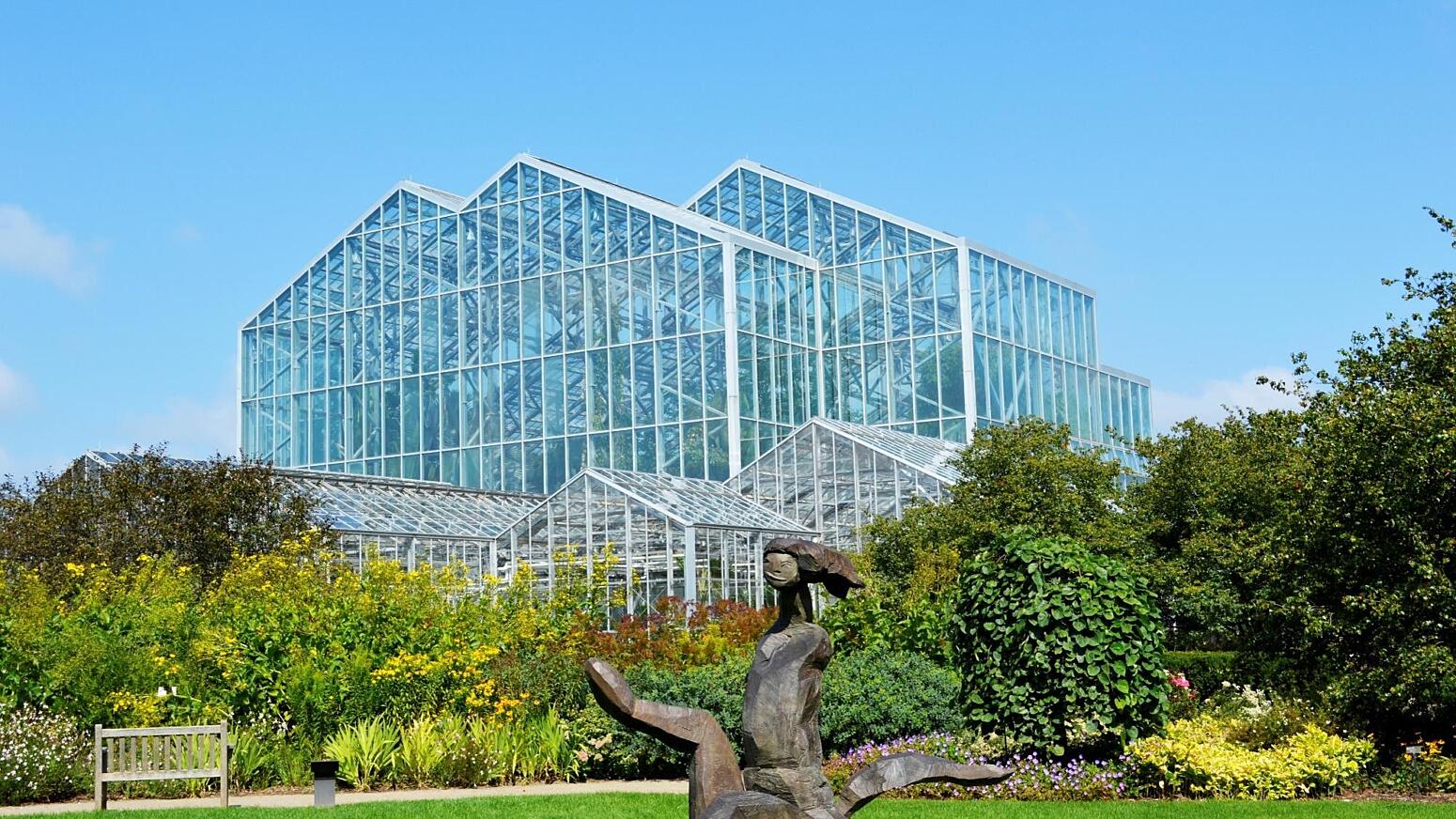
The American Galvanizers Associations 1995 Most Distinguished Excellence in Hot-Dip Galvanizing Award winner, Frederik Meijer Gardens & Sculpture Park opened in April 1995 after 13 years of planning and fundraising by the West Michigan Horticultural Society. The 15,000 square foot, five-story Lena Meijer Tropical Conservatory is the heart of the facility, and houses a waterfall, rock landscapes, and exotic plants.
Galvanizing was selected for this project because of its 'maintenance-free' corrosion protection characteristics. According to the designers, this project would be difficult to paint the first time and maintenance painting would be practically impossible. In addition to structural components, walkway materials, and concrete reinforcing steel were also galvanized. A vital factor to be taken into account in the assessment of a coating system for buildings and structural steel is the relative effectiveness of coatings. No protective coating applied to a structure after completion can provide the same level of maintenance-free protection as a galvanized coating which covers the entire surface of all components, automatically protecting areas to which later access may be difficult or impossible.