Storage
Stacking galvanized articles closely together for extended periods of time, thereby limiting access to freely circulating air, can lead to the formation of a white powdery product commonly called wet storage stain.
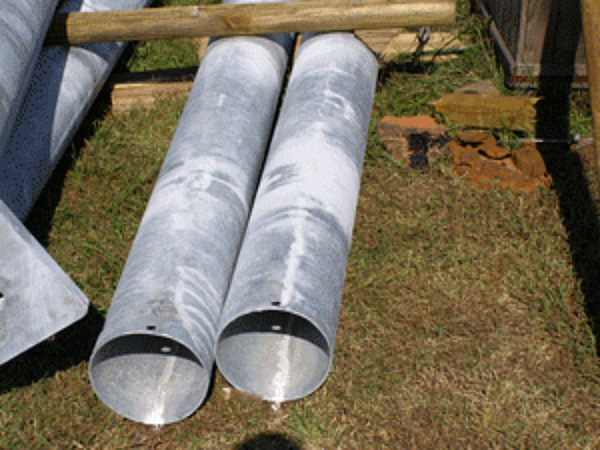
Fabricated assemblies that fully expose the galvanized surfaces to freely circulating air typically do not need a post-treatment to prevent the formation of wet storage stain. Although most after-fabrication hot-dip galvanized products are shipped without any post-treatment, the need for a post-treatment largely depends on the fabrication's configuration and anticipated storage and shipping conditions.
The extent of damage by wet storage stain depends on the duration of exposure to the wet-storage-stain-inducing environment and retained moisture. The attack is accelerated when the retained moisture contains chlorides from seawater, sulfur compounds from industrial environments, or flux residues from galvanizing operations.
To minimize the possibility of wet storage stain, consider these guidelines:
- Whenever possible, avoid nested stacking
- Provide adequate ventilation between stacked pieces
- Incline parts to allow for maximum drainage
- Use spacers and tarp material during shipping if there is the likelihood of condensation or moisture
- Stagger or cross stack galvanized pieces
- Elevate and separate articles stacked outdoors with strip spacers (poplar, ash, spruce)
- Avoid stacking on wet soil or decaying vegetation
- Thoroughly dry small items that are quenched before packing in storage containers
- Include a dehumidifying agent in sealed containers
- Whenever possible, store material under cover in dry, well-ventilated conditions, away from doorways open to the environment
- Ensure the final product is free of flux residues
- Treat with a passivating agent
- Remove road salts from galvanized articles
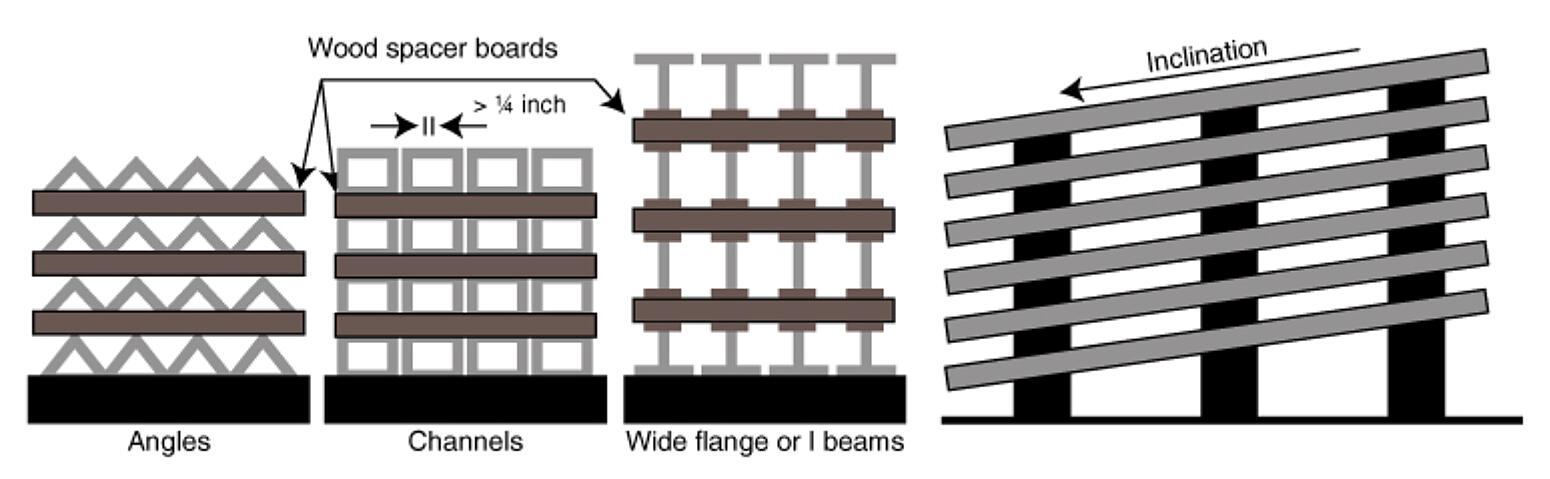
Various surface treatments are available to reduce the possibility of wet storage stain, including:
- Waxes and oils for products such as wire, sheet steel, and fencing
- Passivation treatments
- Duplex or powder coatings
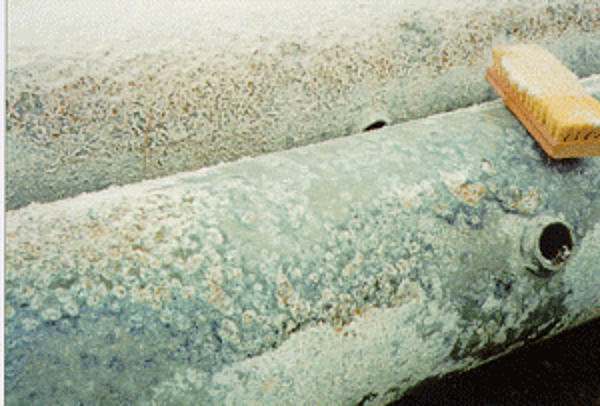
If wet storage stain does form, the objects should be arranged so that their surfaces dry rapidly. Once dry, most stains can be easily removed by brushing with a stiff bristle (not wire) brush. If the affected area will not be fully exposed in service or if it will be subject to an extremely humid environment, even superficial white films should be removed with a soft-bristle brush. This allows for the successful formation of galvanized coatings protective zinc carbonate patina.
In cases where heavy white deposit (above) or red stain has formed because of prolonged exposure to or storage under poor conditions, it must be removed and the damaged area repaired as detailed in ASTM A780. In advanced stages of wet storage stain, the typical white or gray product may blacken. When this occurs, some of the protective coating has been consumed, affecting service-life. Coating thickness tests can be performed on affected areas to ensure that sufficient zinc coating remains after the removal of the wet storage stain. Where the surface staining is light and smooth -as judged by lightly rubbing fingertips across the surface -the stain will disappear gradually and blend with the surrounding surface during normal weathering.