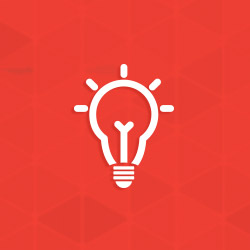
Required vent & drain holes for hollow structural sections & handrail tubing
In order to ensure that all interior and exterior surfaces are protected from corrosion, entire steel fabrications are lowered into and raised out of cleaning solutions, flux solutions, and molten zinc metal. In order to facilitate interior and exterior cleaning and coating, it is necessary to provide holes in fabrications to be galvanized. The primary reason for vent and drain holes is to allow air to be evacuated from within and around the fabrication, allowing it to be completely immersed in the cleaning solutions and molten zinc and for the excess zinc and solutions to drain out and away from the part.
The secondary reason is that if fabrications to be galvanized are not properly vented, cleaning solutions or rinse waters trapped in overlapping or contacting surfaces flash to steam. The resulting pressure increase (up to 3600 psi [25MPa]) can rupture the fabrication. Additionally, trapped moisture that flashes to steam can result in localized uncoated surfaces. Because items being galvanized are immersed in and withdrawn from all cleaning solutions and molten zinc at an angle, vent holes should be located at the highest point and drain holes at the lowest point as mounted during the galvanizing process. A variety of products require vent and drain holes and the size and location are critical to achieve successful and safe galvanizing. The Venting & Drainage page in the Design section includes links for more information and diagrams with examples of good venting and draining.
© 2024 American Galvanizers Association. The material provided herein has been developed to provide accurate and authoritative information about after-fabrication hot-dip galvanized steel. This material provides general information only and is not intended as a substitute for competent professional examination and verification as to suitability and applicability. The information provided herein is not intended as a representation or warranty on the part of the AGA. Anyone making use of this information assumes all liability arising from such use.