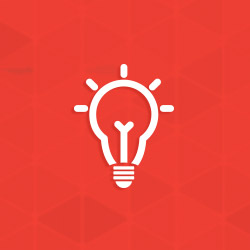
Repairing damaged or uncoated areas of hot-dip galvanized coatings
Although galvanized coatings are highly abrasion resistant, coating damage may occur once the galvanized steel leaves the galvanizers facility due to extremely rough handling, installation techniques, or in-service conditions. Occasionally, small areas of the galvanized article may be bare due to unseen contaiminants the cleaning process is unable to remove. There are methods available to ensure post-galvanizing coating integrity and ASTM A780, Standard Practice for Repair of Damaged and Uncoated Areas of Hot-dip Galvanized Coatings authorizes three accepted touch-up and repair methods:
- Applying zinc-rich paint
- Coating with zinc solder
- Spraying with molten zinc (metalizing)
The touch-up and repair method chosen should consider the specific use of the galvanized steel and the performance characteristics of each of the three methods. Corrosion protection should always be the primary consideration, but certain uses and conditions may warrant selection on the basis of other performance characteristics. Applying zinc-rich paint is often erroneously called cold galvanizing, and may be appropriate for touchup and repair but just as is the case for applying any paint, surface preparation procedures outlined in D6386 should be closely adhered to in order to ensure the best overall performance. It is important to note none of the three repair methods provides the same corrosion protection as hot-dip galvanizing.
© 2025 American Galvanizers Association. The material provided herein has been developed to provide accurate and authoritative information about after-fabrication hot-dip galvanized steel. This material provides general information only and is not intended as a substitute for competent professional examination and verification as to suitability and applicability. The information provided herein is not intended as a representation or warranty on the part of the AGA. Anyone making use of this information assumes all liability arising from such use.