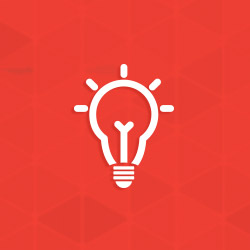
Hydrogen Embrittlement
Hydrogen embrittlement occurs when steel cracks due to hydrogen that is trapped between the grains of the steel. Although steel commonly absorbs hydrogen during the hot-dip galvanizing process, it is usually expelled due to the temperature of the zinc in the galvanizing kettle. In some cases, however, the grain size of the steel is too small to allow release of atomic hydrogen. This can later cause cracking due to increased stress at the location of the hydrogen between the grains. Grains of steels with a tensile strength below 170 ksi (170,000 psi) are usually big enough to allow escape of hydrogen, but for steels having a tensile strength of 170 ksi or greater, there is a potential for hydrogen to remain trapped between grains leading to hydrogen embrittlement.
Hydrogen embrittlement is not observed until the part is under load and can be avoided in several ways. The most obvious way is to ensure the designer has chosen steel with a tensile strength less than 170 ksi. These types of steels have grains large enough to allow escape of any trapped hydrogen. When it is necessary to galvanize high strength steel, a modified galvanizing process can be used to minimize the chances of hydrogen embrittlement. Rather than pickling the steel for the normal length of time, this modified process includes mechanically cleaning the steel, such as by blast cleaning, and then flash pickling (less than 30 seconds in the pickling bath) the steel. Flash pickling is necessary to remove any residues from the blasting operation. This reduces the amount of hydrogen the steel is exposed to and thus reduces the chances of hydrogen becoming trapped in the small grains of high strength steel.
© 2025 American Galvanizers Association. The material provided herein has been developed to provide accurate and authoritative information about after-fabrication hot-dip galvanized steel. This material provides general information only and is not intended as a substitute for competent professional examination and verification as to suitability and applicability. The information provided herein is not intended as a representation or warranty on the part of the AGA. Anyone making use of this information assumes all liability arising from such use.