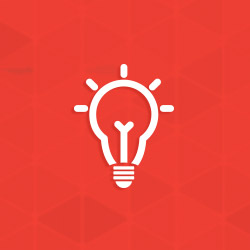
Pickling Steel
What is pickling steel? And, why is it important to galvanizing?
The hot-dip galvanizing process depends on the diffusion reaction between molten zinc and bare steel. It allows a galvanized coating to grow from and adhere to the surface of the steel, providing corrosion protection to the base metal. This diffusion reaction only takes place when the surface of the immersed steel is perfectly clean: entirely free of any oil, grease, metal oxides, mill scale, and rust. The surface of the steel must also be relatively smooth and free of any major defects to produce a high-quality galvanized coating. As such, the cleaning operations prior to the steels immersion in the bath of molten zinc are essential to a galvanizers ability to create a uniform coating with adequate, but not excessive, coating thickness.
After oil, grease, and other organic contaminants are removed from the surface of steel in a degreasing tank, there still remains a thin layer of iron oxide (mill scale) adhered to the steel. In a galvanizing plant, steel will be pickled in an acid tank after the degreasing operation and before pre-fluxing. Acid pickling removes the iron oxides or scales from the steels surface to expose a bare area and permit a galvanized coating to form upon immersion in a molten zinc bath.
Pickling Mechanism
Galvanizers typically encounter one of two types of mill scale dependant on the preparation steps used to manufacture the steel. The high-temperature scale is composed of three layers of iron oxide, and forms after rolling operations at temperatures above 1070F. Low-temperature mill scale consists of two iron oxide layers and develops when steel is heated in an annealing or finishing procedure at less than 1070F. Cracks in either type of scale allow the pickling acid to penetrate the scale layers and dissolve the inner layer, causing the bulk of the scale to be removed in flakes.
After the iron oxides are removed, the steel should be immediately removed from the pickling bath to avoid over-pickling. This is especially true in sulfuric acid baths. Over-pickling is the attack of the bare steel by the acid and can cause a roughening of the whole surface, discoloration of the steel, and a decrease in size and weight of the part. An over-pickled steel surface may also cause an excessively thick galvanized coating.
Types of Acid
Batch hot-dip galvanizers commonly use hydrochloric acid (HCL) or sulfuric acid (H2SO4) for pickling operations in their plant. Very similar pickling rates can be obtained from either choice of acid through a selection of bath temperature and bath strength. Sulfuric acid is generally heated for pickling where hydrochloric acid is used at ambient temperature. Hydrochloric acid is highly volatile so temperatures are kept lower in order to reduce fuming of corrosive vapors. Each choice of acid comes with advantages and disadvantages, they are summarized in Table 1 and Table 2.
Hydrochloric Acid | |
---|---|
Advantages | Disadvantages |
|
|
Sulfuric Acid | |
---|---|
Advantages | Disadvantages |
|
|
Pickling Rates
The rate of steel pickling is affected by the type of acid used, acid concentration, temperature, inhibitor concentration, and agitation. Figure 1 and Figure 2 give examples of possible pickling times based on acid type, concentration, and temperature. The graphs show the time it takes to pickle steel decreases with elevated temperatures in both types of acids. The pickling time in hydrochloric acid is shown to be much faster at 25C but is longer than sulfuric acid at elevated temperatures. The pickling time is also clearly shown to decrease as the concentration of the acid increases. However, the rate of pickling will asymptotically reach a limit as concentration increases. There are other factors that affect the rate of pickling. For information on inhibitors, agitation, and rinsing, please see the American Galvanizers Associations Galvanizing Note Pickling Iron and Steel.
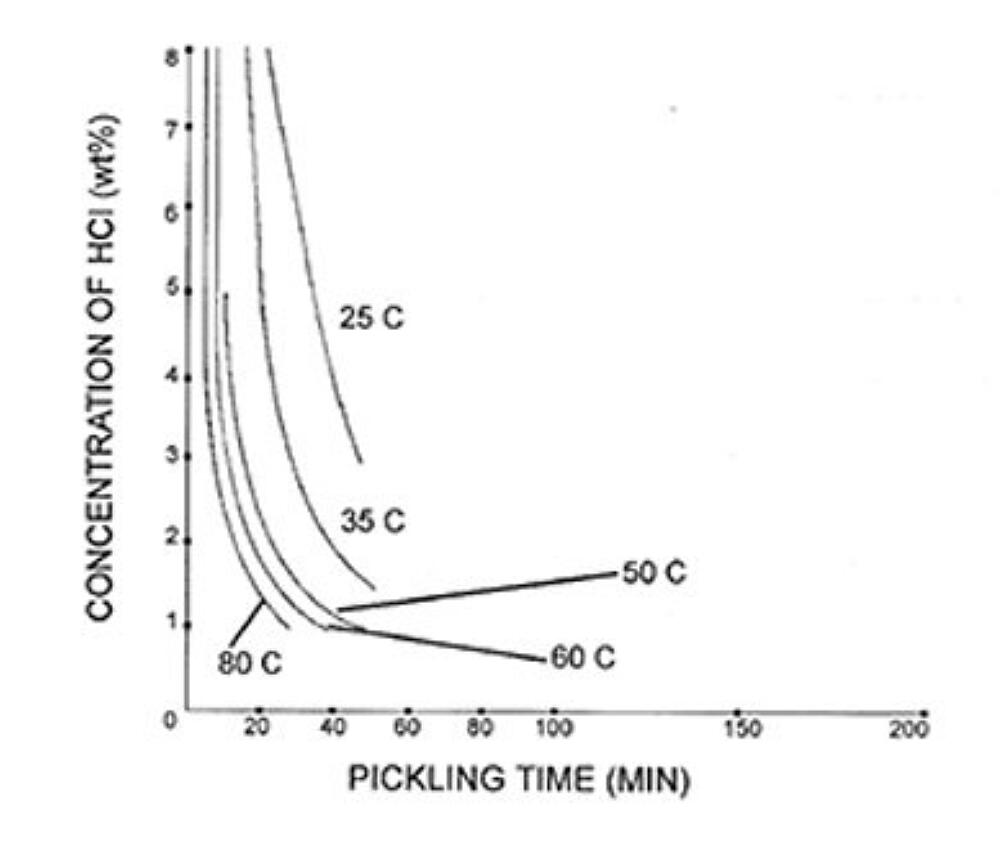
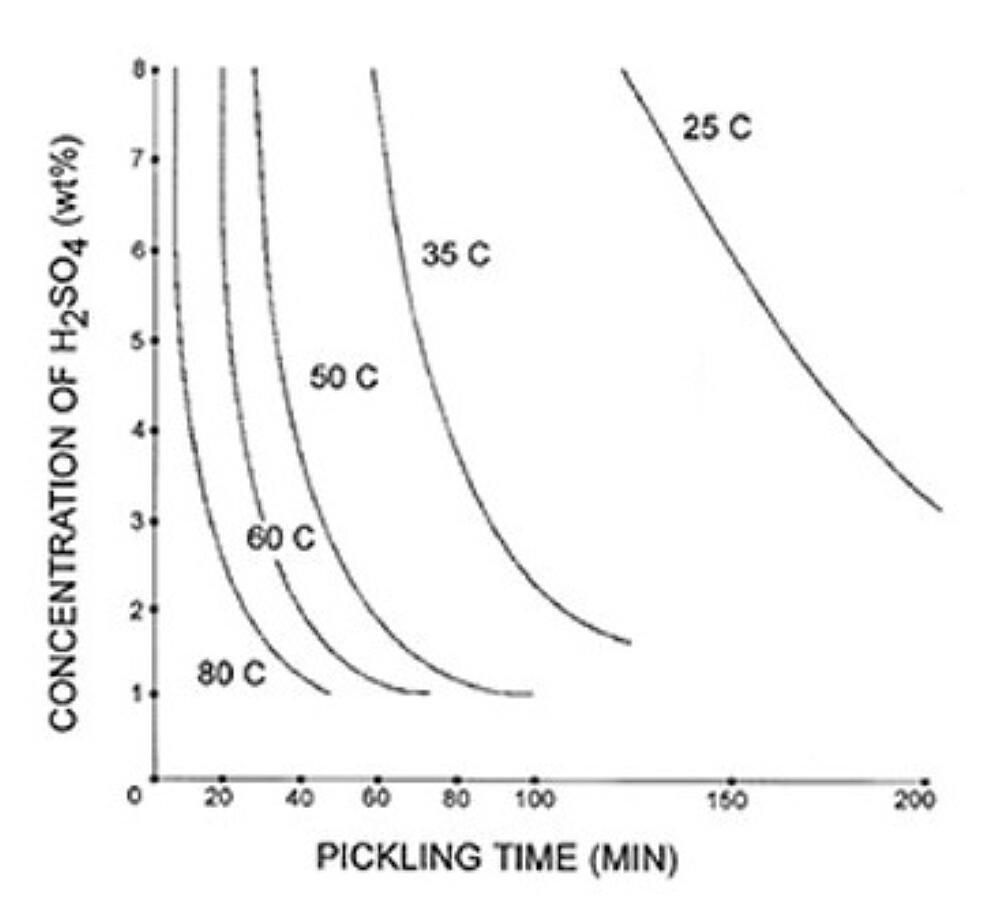
© 2025 American Galvanizers Association. The material provided herein has been developed to provide accurate and authoritative information about after-fabrication hot-dip galvanized steel. This material provides general information only and is not intended as a substitute for competent professional examination and verification as to suitability and applicability. The information provided herein is not intended as a representation or warranty on the part of the AGA. Anyone making use of this information assumes all liability arising from such use.